Modern Slavery Report
Western Glove Works - 2023
1. Introduction
This is the 2023 Modern Slavery Report (“Report”) issued by Western Glove Works (“WGW” or the “Company” or “our” or “we” or "us"), for the activities during the Company’s fiscal year ended September 30, 2023, in accordance with the Fighting Against Forced Labour and Child Labour in Supply Chains Act (S.C. 2023, c. 9) (the “Act"). This Report only covers the activities and actions of WGW.
2. Steps taken to prevent and reduce risks of forced labour and child labour
WGW is committed to protecting human rights and to providing a fair and ethical workplace for its workers. WGW has observed processes that apply globally and that address international human rights standards including the risk of forced labour and child labour in its supply chain, as discussed in further detail within this Report.
WGW respects the standards embodied in the Universal Declaration of Human Rights, the International Covenant on Economic, Social and Cultural Rights, and the International Labour Organization’s Declaration on Fundamental Principles and Rights at Work.
WGW’s Code of Conduct (“COC”) which provides guidelines to ensure the highest standards of respect, integrity, and honesty are applied in WGW’s day to day activities, and a Master Vendor Agreement (“MVA”) which ensures that suppliers comply with minimum internationally recognized standards addressing, among other things, forced labour and child labour.
Further, during the 2023 financial year, WGW engaged with reputable third-party organizations to conduct independent reviews and annual audits of its suppliers.
WGW requires that all suppliers are certified by WRAP, or an equivalent independent regulatory authority.
WRAP’s key principles for evaluating manufacturers promotes responsible business practices and sustainability in supply chain management and contributes to the advancement of the United Nations Sustainable Development Goals (“SDG’s”), in particular SDG 8 (Decent Work and Economic Growth) and SDG 12 (Responsible Consumption and Production).
Furthermore, all suppliers must adhere to WGW’s Code of Conduct and Master Vendor Agreement, which requires all manufacturing be free of forced labour or child labour.
WGW processes are reviewed annually to ensure that forced and child labour in our supply chain is addressed. We strongly oppose forced and child labour and will not knowingly support or conduct business with any entity involved in such activities.
3. Structure, activities and supply chain
Structure
WGW is an apparel company with over one hundred years of experience manufacturing wearable products. Founded in 1921 in Winnipeg, Manitoba, WGW now operates as a partnership between the Silver family, based in Winnipeg, and the Stern Partners group of companies, headquartered in Vancouver, British Columbia.
The Company’s management team, under the supervision of the Board, is responsible for overseeing WGW’s sustainability, social and corporate responsibility, as well as ensuring implementation of and compliance with our Code of Conduct.
Activities and Supply Chain
WGW is a Canadian company, founded in Winnipeg, Manitoba in 1921. It is one of the oldest privately held denim producers in North America. The Company designs, sources, manufactures, and distributes high-quality denim that is marketed and sold across Canada, the United States and Europe. The Company manufactures great fitting jeans and produces approximately 2.5 million units of apparel each year. The Company’s headquarters are in Winnipeg, Manitoba and goods are manufactured in Asia and Southeast Asia, including China, Cambodia, Vietnam, Pakistan, and India.
4. Policies and due diligence processes in relation to forced labour and child labour
In support of our commitment to protecting human rights and to providing a fair and ethical workplace, WGW has processes established that address international human rights standards including the risk of forced and child labour in its supply chain.
i. Code of Conduct
WGW’s Code of Conduct applies in every country and to all factories, employees, officers, and those of its affiliates, and provides the guidelines to ensure that high standards of respect, and integrity are applied in WGW’s day to day activities. The COC also outlines how WGW’s reputation as a good corporate citizen is maintained through the adherence of these high standards. WGW’s core principles embodied in the COC are commitments to promote:
- Compliance with laws, rules, and regulations
- Safe and respectful work environment
- Ethical business practices and behaviors
All suppliers receive WGW’s Code of Conduct, which states that our apparel must be produced without the use of forced labour or child labour. Other topics addressed include:
- Discriminations and human rights
- Health, safety, and the environment
- Compliance with the local laws
- Child labour, Forced labour and Prison labour
- Compensation and benefits
- Legally mandated working hours
- Freedom of Association
- Discrimination and human rights
ii. Master Vendor Agreement
Our Master Vendor Agreement applies to all manufacturers that conduct business with WGW. MVA is an extra layer of due diligence that upholds WGW’s high standards. Among other topics, MVA addresses the following subjects:
- Compliance with the law
- Workplace safety
- Overtime compensation
- WRAP certified or compliance with WRAP principles.
iii. Third-Party Audit
Further to our COC and MVA, WGW requires its suppliers to be vetted and certified by the third-party auditing company Worldwide Responsible Accredited Production (“WRAP”). WRAP is the world’s largest independent certification program focused on the apparel, footwear, and sewn product sectors.
WRAP independently monitors and certifies compliance with 12 key principles, including:
- Compliance with laws and workplace regulations
- Prohibition of Forced Labour
- Prohibition of Child Labour
- Prohibition of Harassment and Abuse
- Compensation and Benefits
- Hours of Work
- Prohibition of Discrimination
- Health and Safety
- Freedom of Association and Collective Bargaining
- Environment
- Customs Compliance
- Security
These standards ensure that WGW’s products are produced under safe, lawful, humane, and ethical conditions. WRAP’s key principles for evaluating manufacturers promote responsible business practices and sustainability in supply chain management and contribute to the advancement of the United Nations Sustainable Development Goals (“SDG(s)”), in particular SDG 8 (Decent Work and Economic Growth) and SDG 12 (Responsible Consumption and Production).
WRAP conducts yearly audits of WGW’s supplier’s factories to ensure standards are being followed. The renewal process requires that factories undergo an audit to ensure continued compliance. Child labour and Forced labour are the top two issues of WRAP’s Zero-tolerance. Any infractions lead to an immediate decertification by WRAP.
To continue to manage risks associated with forced labour and child labour possibilities in our supply chain, WGW, in 2024, will implement a set of new processes that will strengthen its current strategies besides what is already in effect.
- Detailed inquiries and investigations into supply chain components
- Require subcontractors to adhere to our Code of Conduct
- New agreements with correctives measures, that prohibit forced labour and child labour
5. Force labour and child albour risks
WGW has begun the process of identifying the probability of forced labour and child labour risks within its supply chain. Through this process, WGW has identified that there could be a risk that, without our knowledge, manufacturers could subcontract various elements of the production process to unregulated partners that could be employing forced labour or child labour.
Areas of potential-risk activities that WGW has identified could involve the use of subcontractors:
- Trims suppliers: Partners that sell snaps, rivets, zippers, and buttons.
- Yarn suppliers: Producers and suppliers of thread/ raw materials used in WGW’s products.
- Raw cotton providers.
- Packing: Vendors that develop plastic bags and shipping boxes.
WGW is cooperating with its tier one suppliers to assess and put in place processes to monitor subcontractor activities.
- WGW will require all suppliers to adhere to its Code of Conduct
- We will encourage all subcontractors to be certified by WRAP or adhere to its principles
- Have contracts with correctives measures, that prohibit forced labour and child labour
WGW is still in gathering information with respect to assessing our effectiveness in ensuring that forced labour and child labour are not being used in our supply chain.
6. Remediation Measures
In the face of discovering a violation of ethical working practices, WGW has previously attempted remediation measures. In November of 2022, WGW was informed by Transparentem, an international NGO, that an investigation of one of its suppliers had found possible indications of forced labour practices. We had discussions with Transparentem about appropriately compensating workers.
7. Remediation of loss of income
WGW has taken measures with respect to remediating any loss of income resulting from the indication of forced labour brought to our attention by Transparentem. When WGW received Transparentem’s findings about possible unethical labour practices at one of our factories, we asked the assistance of Transparentem and another third-party with remediation, but they indicated that it was not feasible.
8. Employee Training
Employees that work directly with suppliers are trained and act in accordance with the COC which has a zero-tolerance policy on forced labour or child labour. Additionally, employees are aware that WGW requires all suppliers to be certified by WRAP, or another equivalent regulatory body.
Looking ahead, WGW intends to implement mandatory annual training sessions for employees, and factories that will include modules on our COC, ethical behaviour, and civility in the workplace. The COC specifically includes references to child and forced labour as well as international human rights.
Corporate-wide training on the Act and WGW’s approach to ensuring its supply chain is free of any violations will be included in this mandatory annual training in 2024.
9. Assessment Effectiveness
WGW requires its suppliers to be certified by the third-party auditing company WRAP and/or an equivalent regulatory body. The Company is otherwise still at the information gathering stage and will continue to develop its internal capacity and knowledge, and adjust and improve its processes, as required to properly assess the effectiveness of our efforts to prevent forced and child labour.
10. Approval and Attestation
This Report was approved by the board of directors of Western Glove Works Ltd., a partner of WGW, WGW’s fiscal year ended September 30, 2023, pursuant to paragraph 11(4)(a) of the Act.
In accordance with the requirements of the Act, and in particular section 11 thereof, I attest that I have reviewed the information contained in the Report for the entity listed above. Based on my knowledge, and having exercised reasonable diligence, I attest that the information in the Report is true, accurate and complete in all material respects for the purposes of the Act, for the reporting year listed above.
I make the above attestation in my capacity as a director of one of the partners of WGW on behalf of WGW.
Ronald N. Stern
Director
May 27, 2024
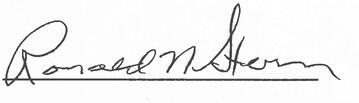
I have authority to bind WGW